Marine Exhaust Gas Heat Recovery Systems
Techno-economic overview of marine exhaust gas heat recovery systems
Marine exhaust gas heat recovery systems can be a useful measure to reduce fuel consumption by 5% for typical cases, with up to 15% for favourable engine and ship characteristics. As a rule of thumb, heat exchangers become more efficient and cost-effective the larger your engine becomes. Conversion of heat to electricity is recommended for diesel-electric vessels, as well as the use of engine cooling water instead of exhaust gas heat. It should be noted that extracting energy and thus cooling the exhaust gas will reduce exhaust back pressure, and can have a negative effect on combustion performance.
EU ETS - carbon tax - greatly influences the economic viability of this system. An EU ETS price of €50 per mT of CO2 can reduce payback time from 5 to 3 years. An EU ETS price of €100 per mT of CO2 can further reduce payback time to 2 years. Use the tool below to learn more.
Contact the helpdesk to clarify your questions about the tool or heat recovery in general
3 Types of heat recovery systems for exhaust gas
A typical marine engine can be several megawatts in size. If one considers that almost half the energy upon combustion is turned simply into heat, that means megawatts of energy are ‘lost’ through a ship’s exhaust pipe. What if you could capture, extract and utilize this energy?
That you can and there are several ways to do so.
Marine exhaust gas heat exchanging devices can take many forms, but they all work on the same principle. Heat exchangers in the exhaust gas channel are used to transfer the ‘waste’ heat energy in the exhaust gases and generate ‘useful’ energy. This can be steam, hot water, electricity or even cool air, as long as it is used for other types of equipment installed on board. For sake of convenience, we have divided heat recovery systems into three different categories.
-
Exhaust gas is used to warm other equipment or appliances on board, most commonly bunker fuel.
One of the most common heat recovery device used in the maritime industry is the exhaust gas boiler (EGB). EGBs are used to generate steam by passing the exhaust gases through a heat exchanger. The heat energy in the exhaust gases is transferred to the water or steam flowing through the heat exchanger, which causes the water or steam to boil and produce steam. This steam is then used to heat cargo or equipment on board the ship, most commonly the bunker fuel (HFO) on board or possibly the main engine. These heat exchangers are available for both main and auxiliary engines, or a combination of two.
Another common heat recovery device is the exhaust gas economizer (EGE), also called exhaust gas heat exchanger (EGHE), which is used to preheat the feed water that is used in the main engine. This can increase the overall efficiency of the engine by reducing the amount of energy that is needed to heat the feed water.
The availability of these systems, plus the fact that they are often required to operate the ship from an economic view, make them commonplace in the marine industry.
-
Exhaust gas is used to create steam or heat a medium which in turn powers a turbine to generate electricity, suitable for diesel electric vessels.
In case electricity is required as useful energy, the steam produced in the exhaust gas heat exchanger can be used to power a steam turbine which produces electricity. Heat exchangers in the exhaust channels are still required to warm the working fluid which in turn drives a turbine to produce electricity.
An efficient way to make use of the low-temperature heat is to apply the Organic Rankine Cycle (ORC). The advantages of this process are its simplicity and maturity. This cycle makes use of an organic fluid (not water) that is vaporized using the heat from the exhaust gases. The vapor then drives a turbine to generate electricity. In addition to using exhaust gas, jacket water heat can be used.
A detailed survey on the use of organic Rankine cycles for waste heat recovery on board ships has been performed by M.E. Mondejar et. al.
Their research concluded that the jacket cooling water and the exhaust gases of the engine are the most suitable heat sources for ORC systems on board ships. Particularly, waste heat recovery from the exhaust gases from engines using low-sulphur fuels can be very promising, with estimated voyage fuel savings of around 10%, although savings of up to 15% are expected.
-
Exhaust gas is used to power a thermos-acoustic device which can convert heat to cold efficiently, suitable for vessels with a high cooling demand.
A more exotic option for heat recovery is the use of thermo-acoustic cooling devices. These devices are quite exceptional and uncommon, but can actually use waste heat to generate sound waves, from which energy is extracted and used to power HVAC systems (Heating, Ventilation, Air-Conditioning).
The conversion efficiency is much higher for these systems as opposed to heat-to-electricity systems, but their applicability is limited to situations where you have a lot of HVAC systems running. This could be the case in warm regions or ship types that need a lot of HVAC systems (such as refrigerated ro-ro vessels).
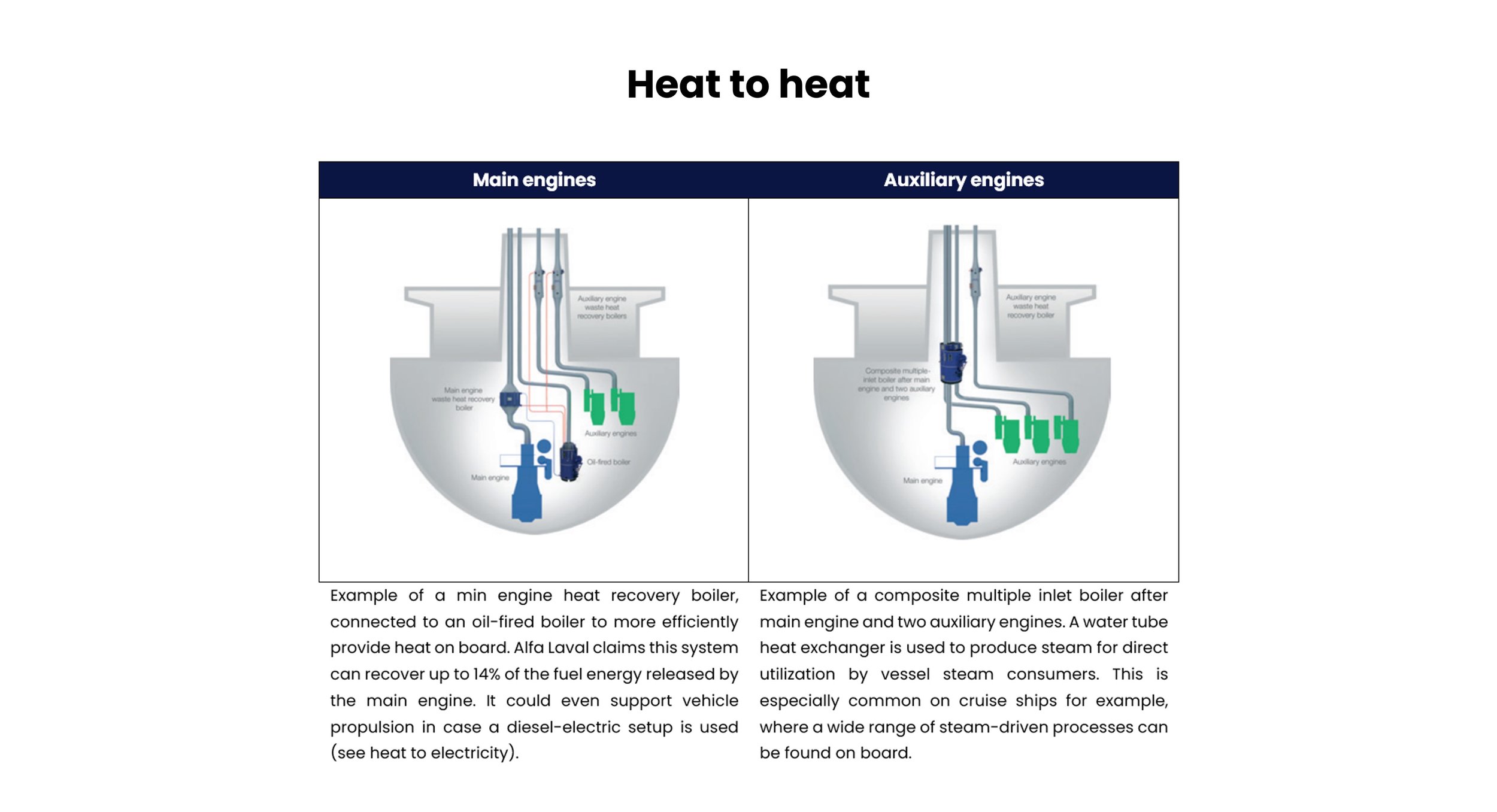
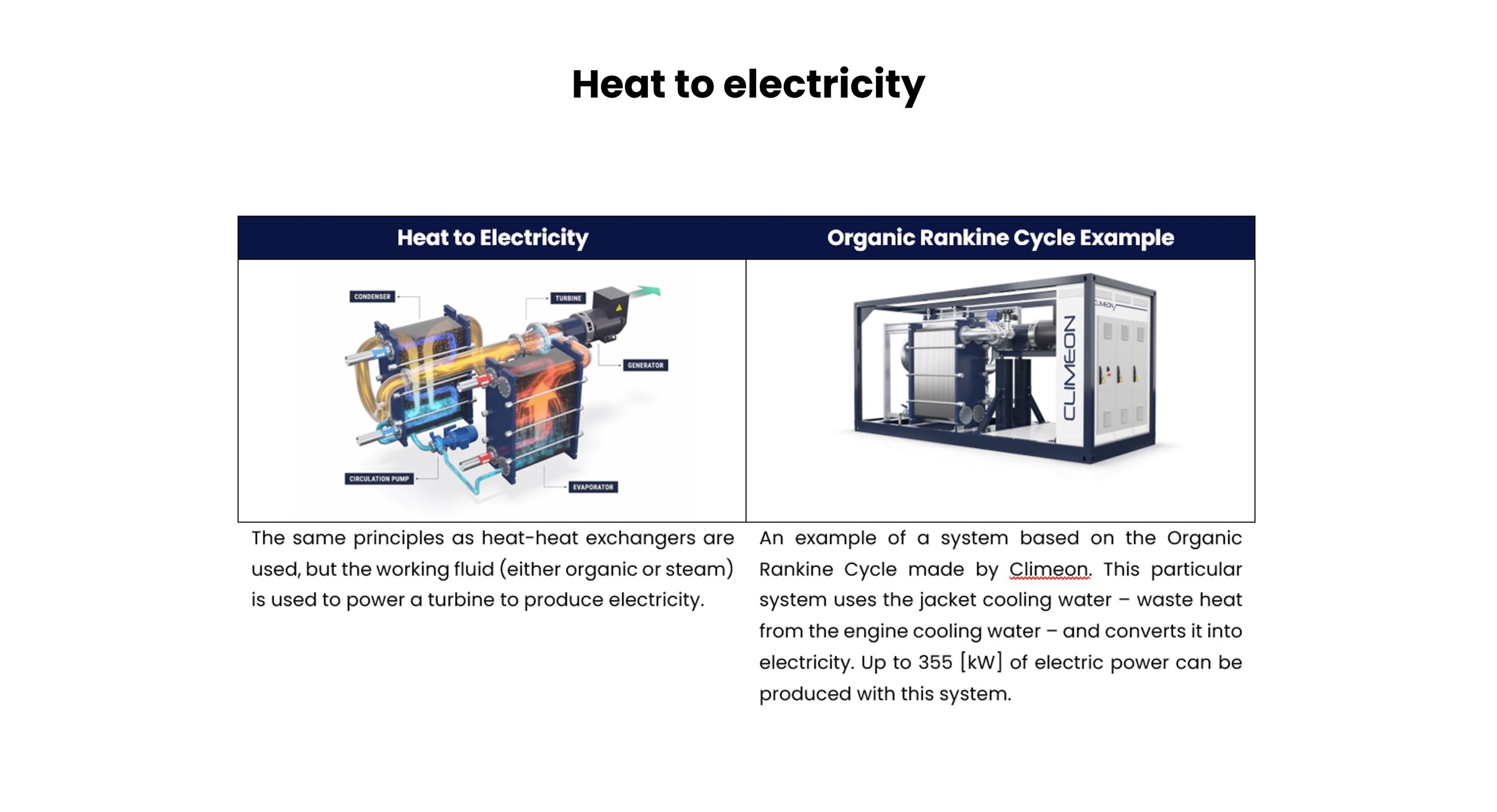
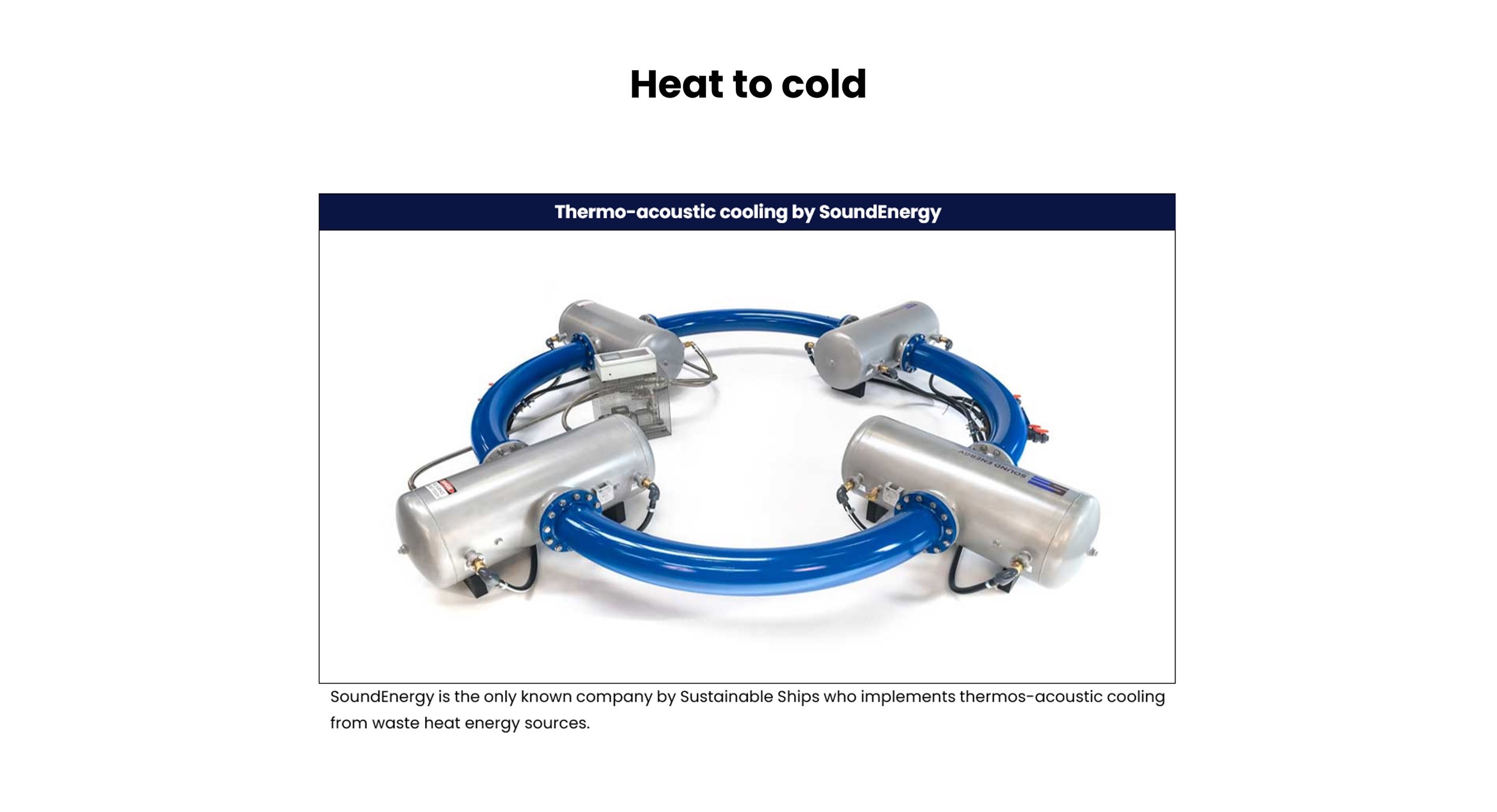
Technical challenges
-
Apart from size or dimensional restrictions in the engine room, one of the main technical challenges for exhaust-based heat exchangers is to ensure correct back pressure in the exhaust system. Back pressure is defined as the exhaust gas pressure that is produced by the engine to overcome the hydraulic resistance of the exhaust system in order to discharge the gases into the atmosphere.
Installing a heat exchanger will interfere with the back pressure of the engine for which it was designed, which can negatively affect engine performance and thus cause an increase in fuel consumption and emissions. The impact of installing an exhaust gas heat exchanger is to be discussed with your OEM.
-
Another challenge is the potential accumulation of soot, and the corrosion of the heat exchanger tubes inside the exhaust gas channel. This can be mitigated by using low-sulphur fuels or tubes that run outside of the exhaust pipe and are warmed by means of conduction only. Though this could reduce efficiency of the overall system, the reduced maintenance costs could make it worth your while.
Economic viability
-
The research from M.E. Mondejar et. al. suggest a payback period of around 2.5 years for bulk carriers and tankers, and 4 years for container ships, considering a fuel price of approximately € 600 per mT. These case studies have been extrapolated into four graphs which can guide in investment decision making, shown below. They show the net present value and payback period for container ships, tankers and bulkers, as well as for the heat exchanger system itself.
From the interactive tool it is clear that carbon tax - EU ETS - has a big influence on your payback period. Use the tool from the top of this page to determine the payback period for your specific case.
-
The below graphs have been transformed into an interactive tool which can be found at the top of this page. The tool allows you to input your desired fuel price, installed power and expected CAPEX investment costs for the heat exchanger system. This interactive tool confirms the results from the research and allows you to make an informed investment decision.
References
Science Direct - A review of the use of organic Rankine cycle power systems for maritime applications
Alfa Laval – Efficiency in boilers and beyond
Dieselnet – Diesel engines back pressure
Climeon – Creating a sustainable future with waste heat recovery
Soundenergy – Thermoacoustic cooling for maritime projects
Glomeep – Exhaust gas boilers on auxiliary engines
CIRSPB – Heating on a ship. Heat exchangers. Ship security systems